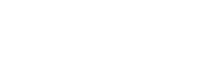
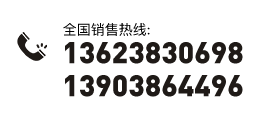
产品特点
1、炉体板金全激光加工,并采用气体保护焊接技术,全模块化装配,摆放稳定,维修方便;工程师经过热力学气密性分析,正常使用10年不变型,不漏火。表面防锈处理,环保水性油漆经久耐用。
2、保温炉体我们采用了目前十年耐用性设计,凹凸镶嵌式炉膛,炉底全铺不沾铝浇注料,专门为坩埚设计了安装平台,确保坩埚稳定水平受力,浇注料采用进口特制的热振性好的材料,全炉采用德国技术二氧化硅等静压纳米保温,导热系数<0.02,同时采用锁温技术的保温棉,正常温降1度时间间隔延长50%。
3、蓄热式高温空气燃烧技术是国内外开始流行的-种革命性的全新燃烧技术,它通过蓄热材料将助燃空气从室温预热至800℃高温,同时大幅度降低(氮氧化物)排放量,使排烟温度控制80℃以下范围,最大限度地回收烟气余热,使炉内燃烧温度更趋均匀。
4、XK1000炉子.上燃烧器功率最大为200KW,目前亦是坩埚炉行业加温速度最快的双蓄热燃烧器,按下按钮后,燃烧系统快速地调整燃烧数据,坩埚内的铝液(铜液、锌液)得到极速的加温,保证能耗的同时实现了加温速度与中频电炉速度基本相当。
5、XK500目前亦是世界上最小的蓄热式燃烧器,我们的工程师通过炉内空气热力学分析,蓄热材料的应用,经过多年的研发,让排烟温度控制在80℃以下范围,革命性的让燃烧效率接近理论值,再创新高!
6、通过一种新扩散燃烧技术,高温炉膛内烟气氮氧化物排放最低至50-80mg/m3,满足于工业炉排放要求。
7、所有动力风机采用变频控制,软件介面包括铝水,炉温温度控制,火力控制,冷炉程序升温曲线保护坩埚,电子空燃比例阀,天然气、液化气一键更换参数等,报警信息看板。软件的升级及现场实用设计出优秀的用户体验。
8、实时精准数字化燃烧控制系统:使用电子脉冲空燃比例技术,使空燃比例精度提高,燃烧室低温与高温燃烧时的智能配比,不管燃气热值、压力波动,系统实时精准调整空燃比,保证100%充分燃烧,无需专业人员维护,亦能长期保证低能耗运行!
9、公司研发出更加可靠的燃气调节装置,取消了电动机构及带皮膜式的比例阀,传统机构长期运行不稳定,高温工作故障极高。新研发的装置包括一个伺服电机+阀体,使用函数算法定位程序,快速反应调整燃气流量,精度及耐用性能远超同行!
10、安全标准严格遵守国家强制措施,包括:断电停气、压力检测、变频联锁、排烟温度保护、阀门位置反馈保护、漏铝水保护、燃气阀门保护等。
11、每台炉二氧化碳排放降低40%,氮氧化物降低50%。实实在在为国家省能源,为企业省成本,为行业做贡献,为客户创价值。为我国早日实现2030年碳达峰提供有利的条件!
工作原理
燃气熔铝炉是使用天然气等燃气为燃料的加热炉,能够利用清洁的燃烧方式,实现燃气炉的高效工作。
目前在铸造行业里常用的燃气熔铝炉主要由坩埚、炉体、烧嘴和排气烟道组成,烧嘴将燃气和空气按一定比例混合燃烧,并将燃烧气体产生的热量送入炉体内对坩埚加热,燃烧的尾气通过排气烟道被排放到大气中,但是燃气熔铝炉产生尾气的热量较高,直接排放会导致较多热量的损失,为此,部分熔铝炉会设置蓄热结构来吸收尾气中的热量,再通过排气烟道将尾气排出。然而,虽然通过蓄热结构进行蓄热,但现有的熔铝炉并不具备能很好地让蓄热后的蓄热结构放热的机构,造成较大的能源损耗。
双蓄热燃气炉技术参数
型号 | BM400/500 | BM800 | BM1000 |
适用压铸机型 | 200-400T | 400-600T | 600-1000T |
标配坩埚尺寸(mm) | Φ780*H750 | Φ880*H880 | ф1030*H830 |
额定容量 | 400/500kg | 800kg | 1000kg |
熔化率 | 160kg/h | 300kg/h | 350kg/h |
天然气流量 | 8-9m3/h | 18-20m3/h | 20-24m3/h |
燃气入口压力 | 天然气/液化气:1Bar=0.1Mpa | ||
天然气管径 | DN25 | ||
空压机气体 | 3-8Bar,8厘管,流量:2方/小时 | ||
电源 | 360V-400+N+G。50-60HZ | ||
用电功率 | 2.2KW | 3.0KW | 4.4KW |
尺寸(L*W*H)(mm) | 2250*1800*2700 | 2200*1900*2700 | 2400*2100*2700 |
炉面高度(H1) | 1100 | 1300 | 1250 |
重量 | 3.5T | 4.0T | 4.5T |
控制柜尺寸(mm) | 600*350*1560 |
近年来材料及天然气价格上涨,铝合金重力铸造行业生产成本也是水涨船高,特别是原材料熔化在生产成本中占比一直很大。在铝车轮铸造生产中,坩埚熔化是其中的一道生产流程。这一过程需要多台坩埚炉进行熔化作业,连续循环工作保证铝水供应。
每台炉子都需要不断重复进行以下生产流程:
加料-熔化-加料-熔化-除渣-精炼-压铸式浇注。
客户在传统重力铸造铝合金坩埚熔化炉生产过程中存在以下三大痛点:
1、熔化铝水时间长,1吨的坩埚炉熔化需耗时2.5小时以上。炉子使用年限越久加热时间越长,直到换埚才稍微有所缩短。由于熔化效率低,客户需要购置数台炉子才能满足生产。
2、坩埚使用时间短,烧损大,破损率高。
3、普通燃气熔炉的耗气量大,吨铝能耗:90-130方天然气,客户需要为此付出昂贵的生产成本。
项目 | 双蓄热燃气炉 | 反射炉(旧炉) |
坩埚容量 | 1吨(共3台连续熔铝) | 1吨(共3台连续熔铝) |
铝合金牌号 | A356(50%铝丝,50%水口) | A356(50%铝丝,50%水口) |
平均加热用时 | 1.8小时 | 2.4小时 |
平均一炉用气量 | 38立方 | 85立方 |
(预留30%铝水) | ||
1个月的生产成品吨平均能耗 | 55立方/吨铝 | 120立方/吨铝 |
烟尘 | 烟尘减少90%,几乎无烟 | 大量烟尘 |
环境 | 废气少温度低,工作环境好 | 大量高温废气,工人难接受 |
钢损率 | 6个月以上 | 3个月 |
双蓄热燃气炉 | 普通燃气炉 |
双蓄热式燃烧技术-高温空气燃烧技术,能耗低 | 传统燃烧技术:没有余热回收非常落后燃烧技术:带热余热回收没技 |
术含量,能耗高 | |
双蓄热式燃烧技术节能巨大,能耗降低至少60~70%,同时大大缓解了大气的温室气体的排放。排烟温度下降到50~80度,带走烟气下降到了10%,手可以直接摸烟气。 | 传统燃烧技术烟气带走了60%热量,余热反射到铝面使整个空气温度超高,工人无法工作。烟气带走40%热量,余热做到最好也有200度排烟,节能效果很差。 |
炉温平均,铝渣减少50% | 烧嘴在一边燃烧,产生局部高温,铝渣多 |
由于燃烧器对称燃烧,炉膛的平均温度增加,加强了炉内传热,在相同产量情况下取汤边温度与接近人放料这边的温度平均,这样产生的铝渣相对减少50%。 | 燃烧器单边燃烧,炉膛的温度在靠近烧咀口边高,无法平均炉内传热,导致在相同产量情况下取汤边温度高,接近人放料这边的温度低,只能人为调高铝水温度熔铝,这样产生的铝渣相对多很多,铝件沾模增加。 |
对称燃烧,炉膛温度低,坩埚烧损减少 | 燃烧局部温度高,风险加大,坩埚烧损增加 |
由于燃烧器对称燃烧,炉膛的气氛温度降低,在相同产量情况下坩埚的导热好,没有局部高温过烧现象,不会随着时间增加影响坩埚导热性能,这样在能耗不增的情况下坩埚的使用寿命增加50%(耐用12个月以上)。 | 燃烧器单边燃烧,炉膛的温度在靠近烧咀口边高达1200度,这样坩埚局部会产生高温结晶,导热率下降,使用6个月以上虽然坩埚没有坏但是能耗升高也得更换,不然能耗成本高得离谱。 |
坩埚使用久了能耗不会涨,升温快 | 坩埚用久了能耗升高,升温慢 |
我们使用一种先进的保温技术,锁温能力超强,随着使用时间的增长而保温性能不会衰减,同时没有局部高温,坩埚不会高温结晶,导热率衰减也非常慢,使用时间过长也不会出现升温慢。 | 只考虑价格便宜,没有考虑耐用性,没有研发,保温性能差,使用不到三个月,能耗直线上升。由于烧嘴单边燃烧,防止坩埚高温结晶,还要停炉旋转坩埚才能有所延期,不然能耗直线上升,使用6个月后能耗高、升温慢,最后得更换新坩埚。 |